The Of Welding Inspection
Table of Contents8 Easy Facts About Welding Inspection DescribedWelding Inspection Can Be Fun For AnyoneSome Known Facts About Welding Inspection.The Buzz on Welding InspectionSome Of Welding InspectionSome Known Details About Welding Inspection Getting The Welding Inspection To Work

2 Elderly Welding Assessor degrees with proficiency including ferrous and nonferrous materials. Our strategy to weld examination as well as surveillance It is crucial to detect any type of problems with welds prior to they rise or not long after they take place so they can be fixed as rapidly as feasible. Aspect's weld inspectors examine the high quality of welds at every step of the manufacture process in the past, during, and after welding.
Customers have varied from private to public and also large to small; the emphasis is constantly on preserving a high standard and also conformity with the relevant code to guarantee that your task has met every one of the needed demands be they code, local, industrial or governmentally enforced laws as well as or demands.
All About Welding Inspection
Swirl existing testing, In eddy current screening, electro-magnetic currents generate a magnetic field that interacts with the subject, creating localised eddy currents. Adjustments in stage and size indicate issues and can be gauged to evaluate size, shape and location. High frequencies are utilized to determine imperfections at or near the surface area, while reduced regularities can penetrate deeper within the test subject.
Numerous characteristics of the weld might be examined throughout a welding evaluation, some about the weld measurements and also others about the use of suspensions of the weld. The dimension a weld may take is vital given that it can directly connect to the weld's resilience and connected effectiveness, little welds may not hold up against stress used while in solution.
The Facts About Welding Inspection Uncovered
These are acnes with or close with the weld, that can or otherwise connect to their measurement and/or area, obstruct a weld from seminar its designed efficiency. Typically, such discontinuities, when are of undesirable measurement or location, are called welding issues and can additionally occasionally trigger early weld falling short though the minimizing of the weld's toughness or though producing tension levels within the aspect of the weld. Welding Inspection.
The most standard purpose is to decide if the weld has a suitable and premium for the made program. To be able to access a weld's high quality, there should be some benchmark to which its attributes can be compared to. It is wrong to try and also access a weld's high quality in the lack of some particular approval needs.
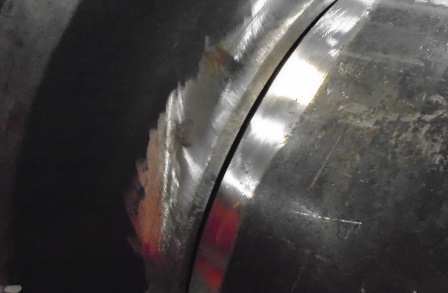
Some Known Questions About Welding Inspection.
This approach is performed in a workshop or area while the welding is being done. The points that are visually inspected consist of the welder's certification, slag removal, joint prep work, weather, present made use of, and problem of the electrode. 2- Magnetic Fragment Evaluating This test is made use of to discover any kind of surface area or barely subsurface problems in a weld.
Bits of iron are after that put on the electromagnetic field and also if there are check any flaws, the particles of decision accumulate around the problem, which reveals where the issue is and also why it happened. 3 Liquid-Penetrant Examining This test will identify defects in the surface of the weld like porosity as well as hairline fractures.
A designer is after that used that will show if any defects show up. 4 Ultrasonic Checking This test is completed by the use audio resonances, which are after that sent through the bonded joint. The signals received on a glass screen will identify if there are any type of problems in the joint of the weld.
4 Easy Facts About Welding Inspection Described
5 Swirl Current Screening This test will certainly reveal incredibly tiny fractures and is completed by the use a round coil that carries rotating currents, which is put near the weld. The rotating currents will certainly create a magnetic area, which will engage with the weld and consequently, create an eddy present.
The resulting imprint size is referred to as a firmness determining table. 8 Devastating Evaluating This test is a harmful examination that is accomplished by reducing the completed weld right into website link items, this is per the code for origin bend, face bend, tensile test, and side bend. It is made use of to find slag addition, porosity, and also undercutting flaws in welds and also is extremely efficient.
This method is done in a workshop or area while the welding is being done. The points that are aesthetically inspected consist of the welder's certificate, slag elimination, joint preparation, climate condition, present utilized, as well as condition of the electrode. 2- Magnetic Fragment Testing This test is used to discover any type of surface area or hardly subsurface flaws in a weld.
Some Ideas on Welding Inspection You Need To Know
Fragments of iron are after that applied to the magnetic field and also if there are any type of defects, the bits of iron will certainly develop around the defect, which reveals where the flaw is and also why it happened. 3 Liquid-Penetrant Checking This test will identify flaws in the surface area of the weld like porosity and also hairline cracks.
A designer is then used that will show if any type of defects show up. 4 Ultrasonic Checking This test is achieved by the use audio resonances, which are then transferred via the welded joint. The signals received on a glass screen will certainly identify if there are any defects in the joint of the weld.
5 Swirl Current Testing This examination will certainly reveal exceptionally tiny cracks and is achieved by the use a circular coil that lugs alternating currents, which is positioned near the weld. The alternating currents will develop an electromagnetic field, which will certainly communicate with the weld and also subsequently, generate an eddy existing.
A Biased View of Welding Inspection
The resulting indentation dimension is described as a firmness measuring table. 8 Damaging Checking This test is a harmful examination that is achieved by cutting the completed weld right into items, this is per the code for origin bend, face bend, tensile test, and also side bend. It is made use of to situate slag inclusion, porosity, as well as undercutting defects in welds as well as is very effective.